Sep 27, 2024
Safety is our number one value
Our goal is for our pipeline and energy facilities to operate safely every day so that the public, our workforce and the environment aren’t affected by an incident involving our assets. Safety is, and always will be, our number one value.
Pipeline safety
We aim for our pipelines and facilities to operate incident-free and to ensure our assets serve our people and communities across the continent for years to come.
Safer, more reliable delivery
Pipelines are the safest, most environmentally friendly way to transport natural gas and petroleum – period. Our pipeline safety programs are among the most robust in the industry and the most important part of our business. From pipeline integrity innovations to investing in leak detection technology and public awareness programs, safety is the common link behind everything we do.
Investing in pipeline safety
One of the best demonstrations of our commitment to safety is our long-standing and ongoing Pipeline Integrity Program. This annual process maintains the integrity, safety and reliable operations of our pipeline systems. Our process includes:
- Risk assessment
- Threat identification and evaluation
- Integrity monitoring to detect pipeline anomalies
- Addressing pipeline anomalies through inspections and repairs
- Additional monitoring, investigative excavation of the pipelines and engineering assessments
- Review and learning.
On top of this program, every kilometre/mile of pipeline, pump, compressor facility or generating station is made using proven technology and integrated, industry-leading safety systems. Once constructed, all pipelines and facilities are monitored constantly, whether that’s from inside the pipe, on the ground or from the air.
Preventing pipeline leaks from end to end
Leak prevention is a top priority. That’s why we take significant steps to prevent the chances of leaks before, during and after our pipelines and facilities are in use.
It begins during construction, with each joint of pipe being factory coated with high-performance coatings and carefully transported to the project location. Each individual weld is inspected using radiographic or ultrasonic techniques to ensure the highest quality welding. Qualified onsite inspectors visually inspect every phase of the installation process including lowering the pipe into the ditch, and then backfilling.
Once installed, a low voltage electrical current is applied to the pipeline to prevent corrosion and the pipe is tested with water (hydrostatic testing), pressurized to a higher level than would be experienced during operation. In the unlikely event of an incident, TC Energy takes full responsibility for emergency response, clean-up and costs.
Read more about our emergency planning.
Proactive detection
24 hours per day, 365 days a year, our Operations Control Centres (OCCs) manage some of the world’s most sophisticated pipeline monitoring technology.
At sites throughout North America, we conduct everything from aerial patrols (using low-flying aircraft and sensitive detection equipment), to geotechnical monitoring and searches for areas where erosion may have washed away the soil covering a pipeline.
In-line inspections are also part of our regular routine. Also known as 'pigging,' (Pipeline Inspection Gauge) these inspections use an internal inspection device called a 'smart-pig' to travel the length of a pipeline to collect data to monitor the condition of the pipeline. When an in-line inspection identifies a potential anomaly, investigative digs may also be conducted to expose the anomaly for further inspection and potential repair.
At the first sign of a potential issue or irregularity, OCC operators stop pipeline flow within minutes, isolating the issue and helping protect the natural environment.
Detecting leaks and maintaining pipe integrity
Learn more about how innovative technology is helping us detect leaks and maintain pipeline integrity across the continent.
CASE STUDY: PSQR Model providing transformational value for asset integrity across our industry
Our Innovation and Decision Optimization (IDO) team developed the Plausible Profiles Corrosion Assessment Model or ‘P Square’ for short, an industry-disrupting model that provides a more accurate representation of corrosion features in pipelines. From its inception in 2014 to today, the P Square Methodology is the first industry-wide improvement to that model in the ensuing 30 years and work is ongoing to incorporate this into referenced standards.
Advancements to the model allow our teams to make better decisions when it comes to preventative maintenance, integrity digs and other integrity activities. As a result, we have realized fewer ground disturbances, with added safety and environmental benefits.
Today, the Psqr Model has taken home numerous awards for its innovative and industry-advancing technology, including a Global Pipeline Award for outstanding advances in innovation and technology related to pipeline transportation.
Constantly investing in new technology
Continually improving the integrity and reliability of our pipelines and facilities is, and always has been, one of our highest priorities. Here are some of the ways we’re doing it.
Ensuring safety
By partnering with industry peers, universities, colleges and governments, we’re part of one of the industry’s largest research and development programs. In fact, since 2013 we have invested more than $150 million towards research and innovation to advance safety, integrity and quality in our industry.
Improving efficiency
For more than half a century, we’ve been instrumental in testing new technologies to maximize pipeline efficiency – from safety improvements to minimizing emissions and more. By focusing our R&D dollars, we’re investing in the long-term sustainability of our operations.
Environmental stewardship
As part of our commitment to environmental stewardship, we work to minimize our environmental footprint as we strive to meet the energy needs of North Americans. We invest heavily in understanding the impacts our pipelines and facilities have on sensitive wildlife species and work to preserve and protect ecosystems throughout North America.
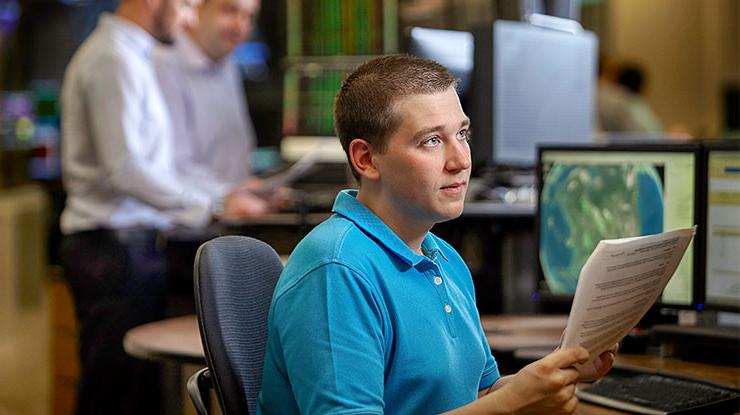
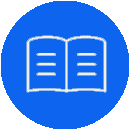
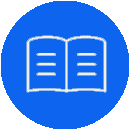
CASE STUDY: Adding ‘ears’ to pipeline monitoring
From our control centre operators to our detailed maintenance and inspection programs and regular ground and air patrols, there are a lot of eyes to ensure our pipelines that deliver the natural gas and oil that fuels our society do so safely. With Hifi’s new fiber optic technology currently being piloted on parts of our Liquids Pipeline System, we now also have ‘ears’ on pipeline monitoring.
Fiber optics ‘hear’ pipeline changes
Two fiber optic lines – one inside the pipeline and one outside – run the length of sections being piloted to provide an additional layer of safety. With data being processed at the speed of light, the fiber optic lines can report changes in pipeline sound, movement and temperature that could result from natural events, such as earthquakes, or man-made impacts such as construction.
With this data, the aim is for pipeline companies to be able to respond more quickly to possible leaks and apply ‘lessons learned’ to prevent future leaks.